Los discos de desbaste desempeñan un papel fundamental en diversas industrias, facilitando el moldeado y el acabado de materiales. Sin embargo, como cualquier otra herramienta, no son inmunes a problemas que pueden afectar su eficiencia y rendimiento. En este artículo, analizaremos en profundidad los problemas comunes de los discos de desbaste, exploraremos sus causas y ofreceremos soluciones eficaces para un flujo de trabajo fluido.
Introducción
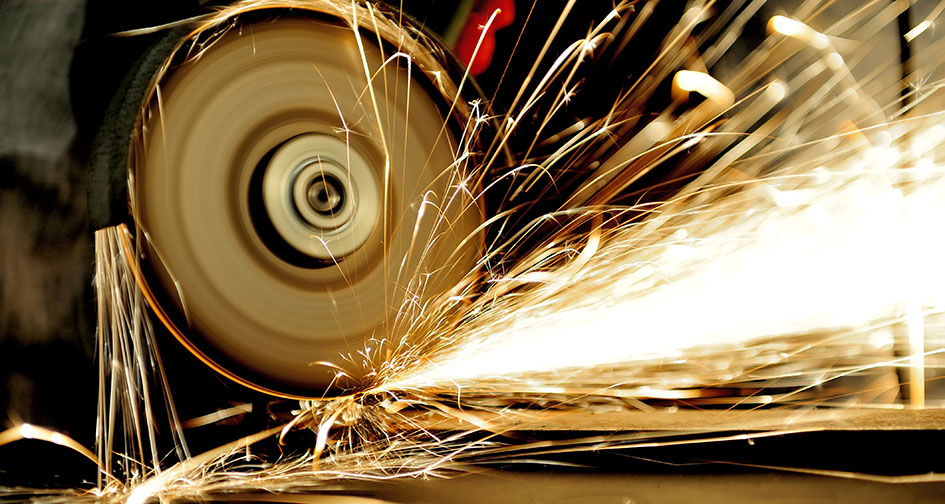
Los discos de desbaste desempeñan un papel fundamental en diversas industrias, siendo herramientas esenciales para los procesos de remoción, conformado y acabado de materiales. Comprender su definición, importancia en las distintas industrias y los problemas comunes que enfrentan es crucial para optimizar su uso y garantizar operaciones eficientes.
A. Definición de discos de rectificado
Los discos de desbaste son herramientas abrasivas que se utilizan en procesos de mecanizado para cortar, desbastar o pulir superficies de materiales. Estos discos suelen consistir en partículas abrasivas unidas a un material de soporte, creando una herramienta giratoria que puede eliminar el exceso de material, alisar superficies o afilar bordes. Vienen en diversas formas y tamaños, cada uno diseñado para aplicaciones específicas.
B. Importancia en diversas industrias
Industria metalmecánica:
En la fabricación y manufactura de metales, los discos de desbaste son vitales para dar forma, desbarbar y acabar superficies metálicas. Se utilizan comúnmente con amoladoras angulares para lograr dimensiones precisas y una calidad superficial óptima.
Industria de la construcción:
Los profesionales de la construcción confían en los discos de pulido para tareas como la preparación de superficies de hormigón, el suavizado de bordes ásperos y la eliminación de imperfecciones en materiales como la piedra y el hormigón.
Industria automotriz:
Los discos de desbaste son esenciales en el sector automotriz para tareas que abarcan desde el afilado de herramientas hasta el conformado y acabado de componentes metálicos. Contribuyen a la precisión y calidad de las piezas automotrices.
Industria de la carpintería:
Los carpinteros utilizan discos de amolar para dar forma y alisar superficies de madera. Estos discos son eficaces para eliminar el exceso de material, refinar formas y preparar la madera para su posterior acabado.
Fabricación general:
Los discos de desbaste encuentran aplicaciones en diversos procesos de fabricación donde se requiere una eliminación precisa de material, contribuyendo a la producción de componentes de alta calidad.
C. Problemas comunes enfrentados
Desgaste y abrasión del disco:
El uso continuo puede provocar desgaste y abrasión del disco de amolar, lo que afecta su rendimiento. Es necesario inspeccionarlo y reemplazarlo periódicamente para mantener su eficiencia.
Calentamiento excesivo:
La fricción excesiva durante el uso prolongado puede provocar sobrecalentamiento, lo que afecta la durabilidad del disco y la calidad de la superficie. Es fundamental mantener una refrigeración adecuada y realizar descansos periódicos.
Atasco:
Los discos de desbaste pueden acumular residuos de material, lo que reduce su eficacia. Limpiarlos regularmente o elegir discos con características antiobstrucción ayuda a prevenir este problema.
Vibración y bamboleo:
Los desequilibrios o el desgaste desigual pueden provocar vibraciones o tambaleo, lo que afecta tanto la calidad del acabado como la seguridad de la operación. Una instalación y un equilibrado adecuados son fundamentales.
Selección de disco incorrecta:
Elegir el tipo incorrecto de disco de desbaste para un material o aplicación específicos puede resultar en ineficiencia y posibles daños. Es fundamental realizar una selección adecuada, teniendo en cuenta la compatibilidad del material.
Comprender la definición, la importancia y los posibles desafíos asociados con los discos de desbaste es fundamental para las industrias que utilizan estas herramientas. Al abordar los problemas comunes y garantizar su uso correcto, las industrias pueden maximizar la eficacia de los discos de desbaste en sus respectivas aplicaciones.
Desgaste de los discos de amolar
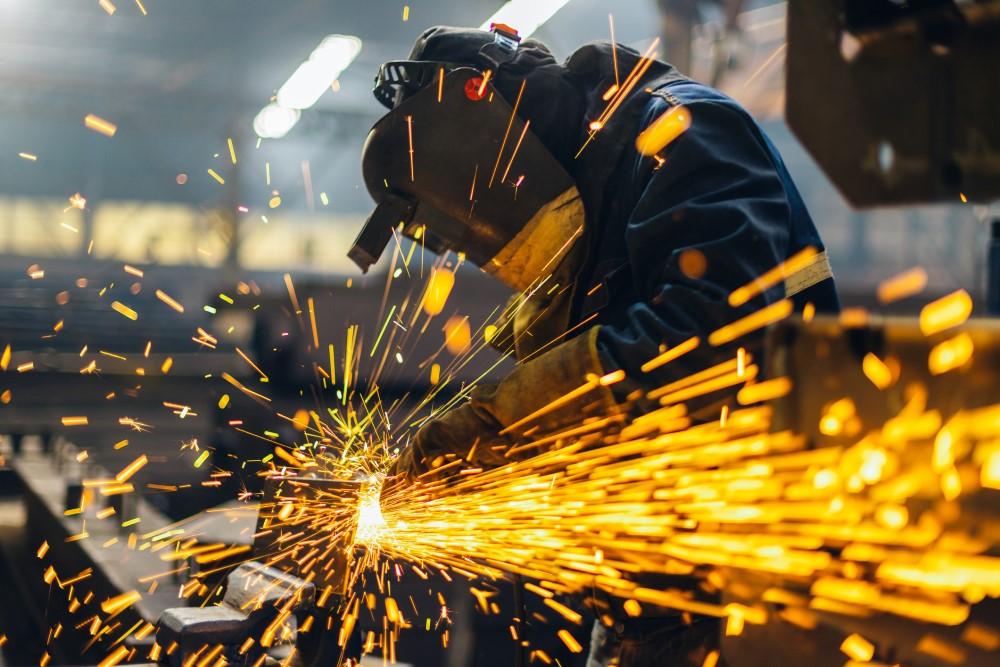
Los discos de desbaste son herramientas esenciales en diversas industrias, ya que proporcionan la abrasión necesaria para tareas que van desde la fabricación de metales hasta el pulido de hormigón. Comprender los factores que contribuyen al desgaste de los discos de desbaste es crucial para optimizar su rendimiento y garantizar la seguridad.
Dureza y composición del material:
Variación de dureza:Los discos de desbaste trabajan con materiales con distintos niveles de dureza. Los materiales abrasivos, como el metal y el hormigón, pueden presentar diferencias significativas en dureza. El desbaste continuo con materiales duros acelera el desgaste.
Composición del material:La presencia de elementos abrasivos en el material a desbastar puede afectar el desgaste del disco de desbaste. Las partículas abrasivas pueden acelerar el desgaste del disco.
Presión y fuerza de molienda:
Presión excesiva:Aplicar una presión excesiva al disco de desbaste puede acelerar su desgaste. Es fundamental usar la presión recomendada para la aplicación específica a fin de evitar una tensión innecesaria en el disco.
Fuerza inadecuada: Por otro lado, una fuerza insuficiente puede provocar un desgaste prolongado, generando fricción y calor adicionales y contribuyendo al desgaste.
Calidad y composición del disco:
Calidad del material abrasivo:La calidad del material abrasivo utilizado en el disco de amolar influye significativamente en su vida útil. Los materiales abrasivos de alta calidad tienden a resistir el desgaste y a mantener el filo durante más tiempo.
Agente adhesivo:El agente aglutinante que une las partículas abrasivas desempeña un papel crucial. Un agente aglutinante bien diseñado mejora la durabilidad del disco.
Condiciones del entorno de trabajo:
Temperatura:Las temperaturas elevadas generadas durante el rectificado pueden afectar la composición del disco. El calor excesivo debilita el agente adhesivo y acelera el desgaste.
Humedad y contaminantes:La exposición a la humedad o contaminantes en el entorno de trabajo puede afectar la integridad del disco de esmerilado, provocando un desgaste más rápido.
Técnica del operador:
Técnica adecuada:La habilidad y la técnica del operador son vitales. El uso inadecuado, como rectificar en ángulos incorrectos o aplicar una fuerza excesiva, puede contribuir a un desgaste desigual y reducir la vida útil del disco.
Inspecciones regulares:Los operadores deben inspeccionar periódicamente el disco de amolar para detectar cualquier signo de daño o desgaste. Los discos que presenten un desgaste superior a cierto límite deben reemplazarse con prontitud.
Compatibilidad de tamaño de disco y RPM:
Talla correcta:Es fundamental usar el tamaño de disco correcto para la amoladora. Los discos de tamaño incorrecto pueden desgastarse de forma desigual o suponer riesgos de seguridad.
Compatibilidad de RPM:Respetar las revoluciones por minuto (RPM) recomendadas para el disco de amolar garantiza un rendimiento óptimo y evita un desgaste prematuro.
El mantenimiento regular, el cumplimiento de las condiciones de funcionamiento recomendadas y la selección del disco de desbaste adecuado para cada tarea son prácticas esenciales para minimizar el desgaste. Al comprender los factores que influyen en el desgaste, los operadores pueden optimizar la vida útil y la eficiencia de los discos de desbaste, contribuyendo así a operaciones de desbaste más seguras y productivas.
Molienda desigual
El rectificado desigual se refiere a la situación en la que la superficie que se está rectificando no logra un acabado uniforme y liso. Este problema puede surgir por diversas razones y afectar la calidad de la pieza de trabajo. A continuación, se presentan los factores comunes que contribuyen al rectificado desigual y sus posibles soluciones:
Selección incorrecta de la muela abrasiva:
Solución:Asegúrese de que la muela abrasiva sea adecuada para el material a desbastar. Cada material requiere propiedades abrasivas específicas. Elija el tipo de muela, el tamaño de grano y el aglomerante adecuados para la aplicación.
Diamantado inadecuado de ruedas:
Causa:Una muela de amolar que no esté correctamente afilada puede provocar un desgaste desigual y un corte ineficaz.
Solución:Rectifique regularmente la muela para mantener su forma y eliminar los residuos acumulados. Un rectificado adecuado garantiza una superficie de corte uniforme.
Líquido de pulido o refrigerante inadecuado:
Causa:El uso insuficiente o inadecuado del líquido de pulido puede provocar un aumento de la fricción y el calor, lo que produce un pulido desigual.
Solución:Utilice un fluido de rectificado o refrigerante adecuado para disipar el calor y reducir la fricción. Una refrigeración adecuada es esencial para obtener resultados uniformes.
Parámetros de molienda incorrectos:
Causa:El uso de parámetros de rectificado incorrectos, como velocidad excesiva, velocidad de avance o profundidad de corte, puede generar un rectificado desigual.
Solución:Ajuste los parámetros de rectificado según el material y los requisitos de la aplicación. Consulte las recomendaciones del fabricante para obtener la configuración óptima.
Muela abrasiva desgastada:
Causa:Una muela abrasiva desgastada puede no proporcionar una superficie de corte uniforme, lo que da como resultado un pulido desigual.
Solución:Reemplace la muela abrasiva al final de su vida útil. Inspeccione la muela regularmente para detectar signos de desgaste.
Presión o velocidad de alimentación desigual:
Causa:Una presión desigual o velocidades de avance inconsistentes durante el rectificado pueden provocar una eliminación irregular del material.
Solución:Aplique una presión uniforme y mantenga una velocidad de avance constante en toda la pieza. La habilidad del operador y la atención al detalle son fundamentales.
Problemas con la máquina:
Causa:Los problemas mecánicos con la rectificadora, como desalineación o problemas con el husillo, pueden generar un rectificado desigual.
Solución:Realice revisiones periódicas de mantenimiento de la rectificadora. Solucione cualquier problema mecánico con prontitud para garantizar su correcto funcionamiento.
Fijación de la pieza de trabajo:
Causa:Las piezas de trabajo mal fijadas o desalineadas pueden provocar un rectificado desigual.
Solución:Asegúrese de que la pieza de trabajo esté correctamente fijada y alineada. Asegúrela firmemente para evitar que se mueva durante el rectificado.
Para solucionar el rectificado irregular se requiere una combinación de configuración adecuada del equipo, parámetros operativos correctos y prácticas de mantenimiento regulares. Los operadores deben estar capacitados para identificar y corregir problemas con prontitud y lograr resultados consistentes y de alta calidad en las aplicaciones de rectificado. Las inspecciones periódicas y el cumplimiento de las mejores prácticas contribuyen a una eliminación eficiente y uniforme del material durante el proceso de rectificado.
Problemas de sobrecalentamiento
El sobrecalentamiento durante el rectificado es un problema común que puede afectar el rendimiento tanto de la muela como de la pieza de trabajo. El calor excesivo puede provocar diversos problemas, como una reducción de la vida útil de la muela, daños térmicos en la pieza de trabajo y una disminución general de la eficiencia del rectificado. A continuación, se presentan posibles causas y soluciones para abordar los problemas de sobrecalentamiento:
Parámetros de molienda incorrectos:
Causa:El uso de parámetros de rectificado inadecuados, como velocidad excesiva, velocidad de avance o profundidad de corte, puede generar un exceso de calor.
Solución:Ajuste los parámetros de molienda dentro del rango recomendado. Consulte las instrucciones del fabricante para obtener la configuración óptima según el material a moler.
Enfriamiento o lubricación inadecuada:
Causa:El uso insuficiente de refrigerante o líquido de esmerilado puede provocar un aumento de la fricción y el calor.
Solución:Asegúrese de contar con un suministro adecuado de refrigerante o lubricante durante el proceso de rectificado. Una refrigeración adecuada ayuda a disipar el calor y previene daños térmicos.
Selección incorrecta de rueda:
Causa:Elegir una muela abrasiva con especificaciones inadecuadas para el material a rectificar puede provocar sobrecalentamiento.
Solución:Seleccione una muela abrasiva con el tipo de abrasivo, el tamaño de grano y la aglomerante adecuados para la aplicación específica. La adaptación de la muela al material minimiza la generación de calor.
Problemas con el material de la pieza de trabajo:
Causa:Algunos materiales, especialmente aquellos con baja conductividad térmica, son más propensos a sobrecalentarse durante el pulido.
Solución:Ajuste los parámetros de rectificado para materiales con menor conductividad térmica. Considere usar una muela de rectificado especializada para materiales sensibles al calor.
Problemas de afilado de ruedas:
Causa:Las irregularidades o un afilado inadecuado de la muela pueden provocar un contacto desigual y acumulación de calor.
Solución:Rectifique regularmente la muela abrasiva para mantener su forma y eliminar cualquier vidriado o residuo acumulado. Unas muelas correctamente rectificadas garantizan un rendimiento de rectificado uniforme.
Mantenimiento inadecuado de la máquina:
Causa:Las rectificadoras mal mantenidas pueden contribuir a problemas de sobrecalentamiento.
Solución:Realice el mantenimiento regular de la rectificadora, incluyendo la revisión de los sistemas de refrigeración, la inspección del equipo de afilado de muelas y la correcta alineación. Solucione cualquier problema mecánico con prontitud.
Flujo insuficiente de refrigerante de las ruedas:
Causa:Un flujo de refrigerante inadecuado hacia la zona de molienda puede provocar una menor disipación del calor.
Solución:Revise y optimice el sistema de suministro de refrigerante. Asegúrese de que el refrigerante llegue correctamente a la zona de rectificado para mantener la eficiencia de refrigeración.
Tiempo de molienda excesivo:
Causa:Las sesiones de molienda prolongadas sin descansos pueden contribuir a la acumulación de calor.
Solución:Implemente un rectificado intermitente y permita descansos para evitar la acumulación excesiva de calor. Este enfoque es especialmente importante para tareas de rectificado grandes o complejas.
Abordar los problemas de sobrecalentamiento durante el rectificado requiere un enfoque integral que incluye la configuración adecuada del equipo, parámetros de rectificado adecuados y prácticas de mantenimiento regulares. Los operadores deben supervisar y controlar la generación de calor durante el proceso de rectificado para garantizar un rendimiento óptimo, una mayor vida útil de la herramienta y resultados de alta calidad.
Preocupaciones por la vibración
La vibración excesiva durante las operaciones de rectificado puede provocar diversos problemas, como una menor calidad de la superficie, un mayor desgaste de la herramienta y posibles daños a la rectificadora. Abordar los problemas de vibración es crucial para lograr procesos de rectificado precisos y eficientes. A continuación, se presentan posibles causas y soluciones para mitigar los problemas de vibración:
Desgaste desigual de las ruedas:
Causa:El desgaste irregular de la muela puede provocar un contacto desigual con la pieza de trabajo, causando vibraciones.
Solución:Inspeccione y afine regularmente la muela abrasiva para mantener una superficie uniforme y plana. Un mantenimiento adecuado de la muela ayuda a minimizar las vibraciones.
Muela desequilibrada:
Causa:Un desequilibrio en la muela abrasiva, ya sea debido a un desgaste desigual o a defectos de fabricación, puede provocar vibraciones.
Solución:Equilibre la muela abrasiva con una balanceadora. El equilibrado garantiza una distribución uniforme del peso y reduce las vibraciones durante el funcionamiento.
Calibración inadecuada de la máquina:
Causa:Una mala calibración o desalineación de los componentes de la máquina, como el eje de la rueda o la mesa de trabajo, pueden contribuir a las vibraciones.
Solución:Calibre y alinee periódicamente los componentes de la máquina para garantizar su correcto funcionamiento. Siga las instrucciones del fabricante para la configuración y alineación de la máquina.
Desequilibrio de la pieza de trabajo:
Causa:Una pieza de trabajo irregular o mal fijada puede crear desequilibrio y provocar vibraciones.
Solución:Asegure la pieza de trabajo correctamente, asegurándose de que esté colocada y sujeta de forma uniforme. Corrija cualquier desequilibrio antes de iniciar el proceso de rectificado.
Selección incorrecta de rueda:
Causa:El uso de una muela abrasiva con especificaciones inadecuadas puede provocar vibraciones.
Solución:Seleccione una muela abrasiva con el tipo de abrasivo, el tamaño de grano y la aglomerante adecuados para el material a desbastar. La adaptación de la muela a la aplicación minimiza las vibraciones.
Desgaste de la máquina:
Causa:Los componentes de la máquina desgastados o dañados, como cojinetes o husillos, pueden contribuir a las vibraciones.
Solución:Inspeccione y reemplace periódicamente las piezas desgastadas de la máquina. Un mantenimiento adecuado ayuda a prevenir vibraciones excesivas y prolonga la vida útil de la rectificadora.
Flujo de refrigerante inadecuado:
Causa:Un flujo insuficiente de refrigerante a la zona de pulido puede provocar acumulación de calor y vibraciones.
Solución:Optimice el sistema de suministro de refrigerante para garantizar una refrigeración adecuada. Una refrigeración eficaz reduce el riesgo de expansión y contracción térmica, que pueden provocar vibraciones.
Problemas con el portaherramientas:
Causa:Los problemas con el portaherramientas o la interfaz del husillo pueden generar vibraciones.
Solución:Asegúrese de que el portaherramientas esté bien montado y alineado con el husillo. Utilice portaherramientas de alta calidad y en buen estado para minimizar las vibraciones.
Fundación de la máquina:
Causa:Una base deficiente de la máquina o un soporte inadecuado pueden amplificar las vibraciones.
Solución:Asegúrese de que la rectificadora esté instalada sobre una base estable y bien diseñada. Resuelva cualquier problema estructural para minimizar las vibraciones transmitidas a la máquina.
Para abordar eficazmente los problemas de vibración durante el rectificado, es necesario combinar el mantenimiento adecuado de la máquina, la selección de muelas y el manejo adecuado de las piezas. Los operadores deben implementar prácticas regulares de inspección y mantenimiento para identificar y resolver los problemas con prontitud, lo que se traduce en un mejor rendimiento y calidad del rectificado.
Problemas de carga durante la molienda
La carga en el rectificado se refiere al fenómeno en el que los espacios entre los granos abrasivos de la muela se llenan con el material que se está rectificando, lo que reduce la acción de corte y aumenta la fricción. La carga puede afectar negativamente la eficiencia y la calidad del proceso de rectificado. A continuación, se presentan posibles causas y soluciones para abordar los problemas de carga:
Material de la pieza de trabajo blanda:
Causa:El molido de materiales blandos puede provocar una rápida obstrucción de los granos abrasivos.
Solución:Utilice una muela de amolar de grano más grueso y estructura abierta al trabajar con materiales más blandos. Esto ayuda a evitar la carga rápida y permite una eliminación eficiente de la viruta.
Contaminación del material:
Causa:Los contaminantes presentes en el material de la pieza de trabajo, como aceites, grasas o residuos de refrigerante, pueden contribuir a la carga.
Solución:Asegúrese de limpiar adecuadamente la pieza de trabajo antes de afilar para eliminar los contaminantes. Utilice fluidos de corte o refrigerantes adecuados para minimizar la carga.
Aplicación incorrecta del refrigerante:
Causa:La aplicación inadecuada o incorrecta del refrigerante puede provocar una lubricación y un enfriamiento insuficientes, lo que produce carga.
Solución:Optimice el flujo y la concentración del refrigerante. Asegúrese de que el refrigerante llegue eficazmente a la zona de molienda para lubricar y enfriar el proceso, evitando así la sobrecarga.
Agudeza de rueda insuficiente:
Causa:Las muelas abrasivas desafiladas o desgastadas son más propensas a sobrecargarse ya que pierden su eficiencia de corte.
Solución:Rectifique y afile la muela de amolar regularmente para mantener su filo. Utilice un rectificador de muelas para exponer los granos abrasivos frescos y mejorar el corte.
Baja velocidad de la rueda:
Causa:El funcionamiento de la muela abrasiva a baja velocidad puede no proporcionar suficiente fuerza centrífuga para expulsar las virutas, lo que genera cargas.
Solución:Asegúrese de que la rectificadora funcione a la velocidad recomendada para la combinación específica de muela y pieza. Una velocidad más alta puede mejorar la eliminación de viruta.
Presión excesiva:
Causa:Aplicar demasiada presión durante el rectificado puede forzar el material hacia la rueda, provocando carga.
Solución:Utilice una presión de rectificado moderada y constante. Ajuste la velocidad de avance para que la muela corte eficientemente sin una presión excesiva que genere cargas.
Especificaciones de la rueda incorrecta:
Causa:El uso de una muela abrasiva con especificaciones incorrectas para el material que se va a rectificar puede provocar cargas.
Solución:Seleccione una muela abrasiva con el tipo de abrasivo, el tamaño de grano y la aglomerante adecuados para la aplicación específica. La adaptación de la muela al material ayuda a evitar la carga.
Limpieza inadecuada del refrigerante:
Causa:El refrigerante contaminado o viejo puede contribuir a problemas de carga.
Solución:Limpie y reemplace el refrigerante regularmente para evitar la acumulación de contaminantes. Un refrigerante fresco y limpio mejora la lubricación y la refrigeración, reduciendo la probabilidad de sobrecarga.
Técnica de vestimenta inadecuada:
Causa:Un afilado incorrecto de la muela abrasiva puede provocar irregularidades y sobrecargas.
Solución:Rectifique la rueda correctamente con la herramienta adecuada. Asegúrese de que el perfil de la rueda sea uniforme y sin irregularidades para evitar la carga.
Para abordar eficazmente los problemas de carga, es necesario combinar la selección correcta de muelas, la configuración de la máquina y las prácticas de mantenimiento. Los operadores deben seguir los procedimientos recomendados, utilizar parámetros de rectificado adecuados e implementar un afilado regular de muelas para minimizar la carga y optimizar el rendimiento del rectificado.
Elegir el disco de desbaste adecuado es crucial para obtener resultados óptimos en diversas aplicaciones de metalistería y fabricación. La selección depende de factores como el material a trabajar, el acabado deseado y el tipo de amoladora utilizada.
Cómo elegir el disco de amolar adecuado
Compatibilidad de materiales:
Metales ferrosos (acero, hierro):Utilice discos de desbaste diseñados específicamente para metales ferrosos. Estos discos suelen contener abrasivos adecuados para la dureza del acero y son menos propensos a la carga.
Metales no ferrosos (aluminio, latón):Elija discos con abrasivos adecuados para metales más blandos para evitar obstrucciones. Los discos de óxido de aluminio o carburo de silicio son opciones comunes.
Material abrasivo:
Óxido de aluminio:Ideal para el desbaste general de metales ferrosos. Es duradero y versátil.
Alúmina de zirconio:Ofrece una mayor eficiencia de corte y longevidad, lo que lo hace adecuado para el pulido agresivo de metales ferrosos y no ferrosos.
Carburo de silicio:Ideal para amolar metales no ferrosos y piedra. Es más afilado, pero menos duradero que el óxido de aluminio.
Tamaño de grano:
Grano grueso (24-36):Eliminación rápida de material y rectificado de alta resistencia.
Grano medio (40-60):Equilibra la eliminación de material y el acabado de la superficie.
Grano fino (80-120):Proporciona un acabado suave, adecuado para la preparación de superficies y el pulido ligero.
Tipo de rueda:
Tipo 27 (Centro deprimido):Disco de desbaste estándar con superficie plana, ideal para desbaste de superficies y trabajos de cantos.
Tipo 29 (Cónico):Diseño en ángulo para una eliminación agresiva de material y una mejor combinación de superficies.
Tipo 1 (Recto):Se utiliza para aplicaciones de corte. Proporciona un perfil delgado para un corte preciso.
Solicitud:
Molienda:Discos de desbaste estándar para eliminación y conformación de material.
Corte:Utilice discos de corte para cortar metal, proporcionando un borde recto y limpio.
Discos de láminas:Combina pulido y acabado en uno. Ideal para difuminar y alisar superficies.
Compatibilidad con Grinder:
Asegúrese de que el disco de amolado sea compatible con el tipo y la velocidad de la amoladora que se utiliza. Consulte las recomendaciones del fabricante para conocer las RPM (revoluciones por minuto) máximas del disco.
Especificidad de la tarea:
Eliminación de material pesado:Elija un grano grueso y un disco tipo 27 o tipo 29 para eliminar el material de manera eficiente.
Acabado de superficies:Opte por granos medianos a finos con discos de láminas para obtener acabados más suaves.
Consideraciones de seguridad:
Siga las pautas de seguridad, incluido el uso de equipo de protección personal (EPP) adecuado, como gafas y guantes de seguridad.
Elija discos reforzados para mayor durabilidad y seguridad.
Marca y Calidad:
Seleccione discos de marcas reconocidas por su calidad y consistencia. Los discos de alta calidad ofrecen mayor rendimiento y durabilidad.
Consideración de costos:
Equilibre el costo inicial con la vida útil y el rendimiento esperados del disco de desbaste. Los discos de alta calidad pueden tener un costo inicial más alto, pero ofrecen una mejor relación calidad-precio a largo plazo.
Al considerar estos factores, los operadores pueden elegir el disco de pulido adecuado para sus aplicaciones específicas, garantizando eficiencia, seguridad y resultados óptimos.
Conclusión
En conclusión, seleccionar el disco de desbaste adecuado es fundamental para obtener resultados exitosos en metalistería y fabricación. La elección depende de diversos factores, como el material a trabajar, el acabado deseado y el tipo de amoladora utilizada. Al considerar la compatibilidad del material, el tipo de abrasivo, el tamaño del grano, el tipo de muela, la aplicación, la compatibilidad de la amoladora, la especificidad de la tarea, la seguridad, la calidad de la marca y el costo, los operadores pueden tomar decisiones informadas para mejorar la eficiencia y la seguridad en sus procesos de desbaste.
Es fundamental cumplir con las normas de seguridad, usar el equipo de protección personal adecuado y seguir las recomendaciones del fabricante sobre la compatibilidad de la amoladora y el disco. Ya sea para la eliminación de material pesado, el acabado de superficies o aplicaciones de corte, el disco de amolado adecuado puede influir significativamente en la calidad y la eficiencia del trabajo.
Además, los controles periódicos de desgaste, el abordaje de problemas como el sobrecalentamiento y las vibraciones y la comprensión de los problemas de carga contribuyen a prolongar la vida útil del disco de amolar y garantizar un rendimiento constante.
En resumen, un enfoque sistemático y bien informado para seleccionar, usar y mantener los discos de pulido es clave para lograr resultados óptimos, mejorar la productividad y garantizar un entorno de trabajo seguro.
Hora de publicación: 12 de enero de 2024